Fuente:
AQUIHola a tod@s
...No se me ocurriría comprimir el gas de brown, salvo que la vida ya no tuviese sentido y esas cosas. Es tremendamente peligroso!!!, bastaría una pequeña descarga de electricidad estática para que volase todo por los aires.
...No, la idea es quemar el gas conforme se produce, reduciendo al mínimo la acumulación del gas en el proceso. El problema consiste entonces en producir suficiente cantidad de gas por unidad de tiempo como para alimentar el soplete. Como en los soldadores que construye y comercializa Ricardo Cardo
www.freewebs.com/intermecanicaOs cuento como van los experimentos...
Acabe la célula electrolitica, Hecha con la basura que tenia por ahí, como se puede ver por la irregularidad de las placas. La distancia entre las placas es ce 1 cm, muy lejos de la distancia óptima, pero me daba miedo el consumo. Las placas están conectadas, una si, una no, a cada electrodo, aisladas con rebanadas de tubo (verde) de 1cm.
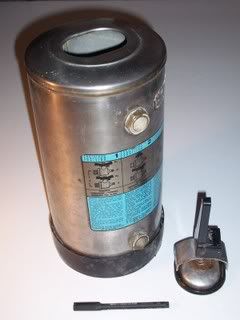
La cuba tuvo que ser este descalcificador de cafetera de bar (porque no tenía otra cosa a mano). Montar la célula electrolitica dentro fue como construir un barco en una botella, porque apenas me pasaba la mano por la abertura. Tuve que hacerme útiles para poder apretar las tuercas interiores. La forma ideal que imaginé para la cuba fue con una olla a presión y electrodos concéntricos, pero las ollas valen mas de 40€ y aun no he encontrado ninguna en el chatarrero.
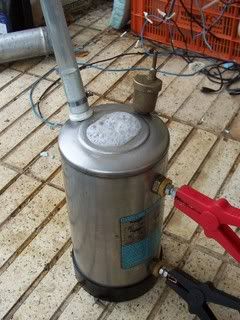
En la siguiente foto podéis ver la cuba electrolítica en marcha, conectada a una batería de coche. Por la tapa abierta se ven las burbujas del gas. Tiene montados dos sistemas que se me ocurrieron para mantener la cuba a presión y evitar la acumulación de una burbuja de gas en el interior de la cuba.
El primero es simplemente un tubo cuyo extremo libre esta colgado a una altura de tres metros. Es transparente para monitorizar lo que esta pasando en el interior de la cuba. Con la cuba cerrada lo lleno hasta que la columna de agua llega a los dos metros, para asegurar una presión mínima. (que ahora me da que no será suficiente).
El segundo es un desgasificador de calefacción, tiene una boya interna que acciona una válvula. Impide el paso del liquido pero no del gas. Cuando se forma una burbuja en el interior baja la bolla y permite la salida del gas.
-------------------------------------------------------------------------------------
Como ya os conté, hice algunas pruebas que me hicieron pensar que podría hacerlo funcionar con la soldadora de arco eléctrico. Os cuento como fue el experimento.
Primero necesitaba un rectificador capaz de aguantar la potencia de la soldadora, de unos 180A de pico y unos 40A de flujo constante. Así que monte este hecho con 10 puentes de diodos KBPC3510, (35A a 1000v) 350A teóricos. Está un poco sobre dimensionado pero no me la quería jugar ajustando demasiado, si se cruzase uno rompería los demás. Los fabricantes te dan las características del componente como valores máximos de carga, y no como valores de trabajo habitual.
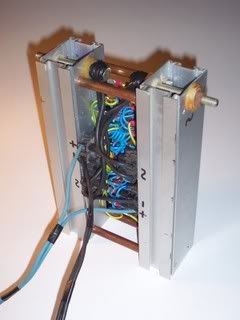
En las fotos lo podéis ver a medio montar y ya montado.
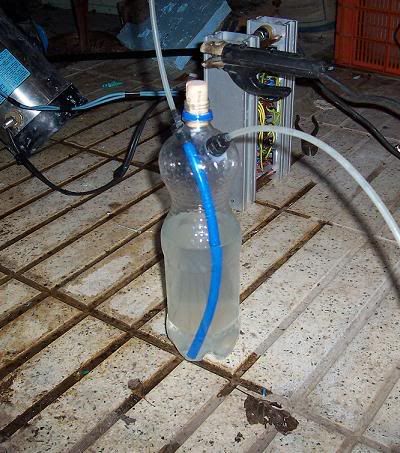
También monté un sistema de seguridad intermedio, consistente en una botella por la que tiene que burbujear el gas que sale de la cuba. Si se cuela la llama por el conducto que lleva hasta la botella, esta explota haciendo saltar el tapón de corcho, pero al estar el tubo que va hasta la cuba sumergido en el agua, queda protegido de la explosión y la llama no puede continuar. Además También cuento con los sistemas de protección del mismo soplete (un arrestallamas de cobre poroso, y una válvula anti retorno)
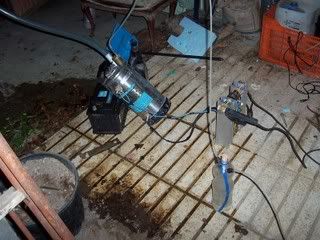
En esta foto podéis ver el sistema burdamente montado para hacer pruebas.
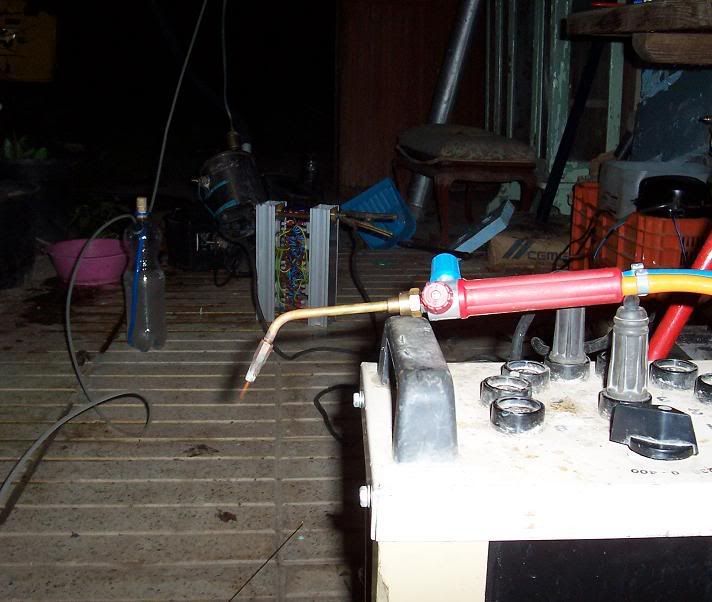
Y en esta el soplete funcionando con el gas de brown generado por este sistema.
(Disculpad la calidad de estas fotos)
El resultado fue:
Que con la soldadora funcionando en la mínima potencia conseguía una cantidad de gas claramente insuficiente para alimentar el soplete. Solo servía para colocar la boquilla más pequeña y soldar pequeñas piezas.
Con la soldadora funcionando a media potencia conseguía una llama de unas 2cm capaz de fundir sin problemas la varilla de aportación, pero incapaz de mantener una pieza de 4mm de grueso de acero inoxidable a la temperatura necesaria para soldar con plata.
Con la soldadora funcionando a toda potencia conseguía una llama de unos 4cm de largo, y empezaba a tener potencia para soldar, pero la soldadora se calentó peligrosamente y en 5 minutos la tuve que parar por peligro de estropearla.
La tensión de alimentación en la cuba oscilaba entre 2,3v con la mínima potencia y 2,5v con la máxima. La tensión de alterna a la entrada de los rectificadores oscilaba entre los 4,3v con la mínima potencia y los 4,7v con la máxima potencia capaz de dar la soldadora.
Si contamos que la soldadora en “abierto” da una tensión que oscila entre los 20V y los 40V veremos que la cuba electrolítica “amorra” a la soldadora, es decir, que absorbe mucha más potencia de la que es capaz de suministrar la soldadora.
El consumo a la máxima potencia oscilaba entorno a los 1.800w, y el consumo de la cuba a 2,5v debía de ser de superior a los 40A que es capar los de suministrar la soldadora. Gran parte de la energía consumida se debía de convertir en calor en la propia soldadora, al estar sobrecargado el transformador.
La cuba apenas se calentó durante las pruebas.
Llegado a este punto creo que me quedan 4 opciones.
Conseguir una soldadora más grande..., inviable económicamente.
Construir un transformador capaz de alimentar la cuba con, por lo menos, 80A a 2v... No lo sé, tengo un par de transformadores de 3000W que tal vez pueda modificar, ya os contaré. Pero es una opción difícilmente reproducible, y me gustaría poder encontrar un sistema que podáis montar todos los que estáis interesados en este post.
Construir una célula electrolítica capaz de funcionar a 220v... Esta parece a priori una buena opción, el problema es que con los datos que aportaba Maca, tendría que tener 100 electrodos de entre 8 y 10 cm de lado para trabajar entre 12 A y 20A a 2,2v entre placas , que supongo sería el margen de intensidad necesaria para producir más o menos el doble de gas que con el prototipo actual. Si contamos comprar abundante chapa de inox en el chatarrero y los discos de corte necesarios, me imagino se ira sobre los 40 o 50 €. Aquí topamos con un problema económico coyuntural, estamos a fin de mes y estoy arruinado... Ya veremos como se presenta la economía de diciembre.
Abandonar el proyecto y comprar el oxigeno para el soplete... inviable también económicamente, además de emocionalmente.
Ya os contaré nuevas.
Y si, por favor, alguien tiene algún consejo, bienvenido sea...
Un saludo